Now that NFPA 1006 Standard for Technical Rescue Personnel Professional Qualifications (2017 edition) has been in place for a while, it’s a good time to revisit the changes that have been made. While we won’t go into every single change from the previous 2013 edition, we will cover some of the more significant ones – particularly for the specialty areas that we deal with most.
So, let’s get to the big changes right off the bat. As you are probably aware, there was a big disconnect between NFPA 1006 and NFPA 1670 Standards on Operations and Training for Technical Search and Rescue Incidents. While there are technical committees for the development of both 1006 and 1670, very few committee members sit on both committees. The need for a correlating committee became apparent, and it is that correlating committee that coordinated and at times arbitrated changes to both standards in an effort to marry them up.
For example, NFPA 1006 Levels I & II have been replaced with Awareness, Operations and Technician levels to correlate with 1670 performance levels. This change may seem minor, but it allows for (and provides guidance in) training auxiliary personnel to a level of competency to support the Technical Rescue Team. This is reflected in the title change of 1006 from “Standard for Technical Rescuer Professional Qualifications” to “Standard for Technical Rescue Personnel Professional Qualifications.”
This change provides the option to train a team to a level for handling less technical incidents and still meet the standard for that level of proficiency. It also allows for a level of competency to begin a rescue effort while awaiting a more technically trained and equipped team to respond. This aids teams that do not have the manpower, equipment or funding to train to the Technician level by providing performance goals for Operations and Awareness levels.
NFPA 1006-2017 has also added several new specialty areas to include: Floodwater Rescue, Animal Rescue, Tower Rescue, Helicopter Rescue, and Watercraft Rescue. Several new definitions have been added to correlate with NFPA 1670. Clarification is provided by further defining dive operations, search, watercraft, wilderness, and other terms. You will also find that the word “search” (as used in the title of 1670) has been incorporated into many of the specialty areas of 1006 – another attempt to better correlate the two standards.
Again, we have attempted to highlight some of the key changes in NFPA 1006-2017. We think the modifications will make it easier to understand what is required of technical rescuers as well as auxiliary support personnel. As always, we encourage you to read the standard in its entirety. If you have any questions, please call us at 800-647-7626.
Changes to NFPA 1006 That May Affect Your Operations and Training
Why is LOTO So Important?
Foundry Fined for Confined Space Amputation Accident
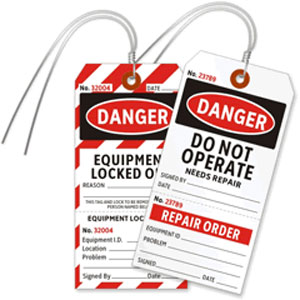
Two workers were cleaning and unjamming a 38-foot long auger screw conveyor at the bottom hopper of an industrial air filtration device without effectively de-energizing or locking out the equipment.
One of the workers re-entered the 20-inch square opening after the cleaning was done to retrieve a work light from inside the confined space, when a maintenance worker 45 feet away energized the equipment to perform a test.
The moving auger screw pulled the worker into the screw conveyor. Both his legs had to be amputated in order to free him.
“Sending a worker into a confined space is dangerous, especially inside machinery that can be powered on at any time,” said Cal/OSHA Chief Juliann Sum.Employers must ensure that machinery and equipment are de-energized and locked out before workers enter the space to perform operations involving cleaning and servicing.
Cal/OSHA’s investigation found that:
• The foundry did not have a permit-required confined space program.
• The screw conveyor was not de-energized and locked out before workers entered the hopper, and accident prevention signs were not placed on the controls.
• The worker re-entering the hopper was not monitored by a confined space attendant.
• The foundry lacked specific procedures for de-energizing and locking out the equipment.
Cal/OSHA issued eight citations with proposed penalties totaling $283,390. The eight violations cited included one willful serious accident-related, one willful serious, four serious, one willful general and one general in nature.
Source: www.dir.ca.gov News Release No.: 2018-15 Date: March 7, 2018
New Pocket Guide from Roco
Newly revised and updated with 82-pages of color drawings and detailed illustrations, Roco's new Pocket Guide features techniques taught in our rescue classes. Made from synthetic paper that is impervious to moisture makes this pocket-sized guide the perfect reference during training or on the scene.
Pocket Guide features: Knots - Rigging - Patient Packaging - Lower/Hauling Systems - Tripod Operations - Low Angle - Pick-off Rescue - High-lines - Confined Spaces and much more.
Reference charts include: Confined Space Types, Suspension Trauma, and Rescue Gear Service Life Chart.
Click here to order your copy today!!
Another Preventable Confined Space Fatality
Comments by Dennis O'Connell, Roco Director of Training & Chief Instructor
The following “OSHA Fatal Facts” is another example of simple safety procedures not being followed or having no procedures in place.
Whether you’re in the refinery, chemical plant, agriculture, shipyards, construction or municipal fields, all of us have an obligation to protect ourselves, our employees and those we work with.
In this case, a fairly harmless looking tank and product resulted in another confined space fatality. As I’ve said many times before, using proper air monitoring techniques is probably the one thing you can enforce that would have the greatest impact on reducing fatalities. This tragic story is another example.
It’s also important to note that while there are different standards for different industry segments, they all attempt to lead us down the same path in using appropriate safety precautions – particularly, in this case, when entering confined spaces. We must remember that these specific standards have all grown from the General Duty Clause, as cited in this article. Basic and to-the-point, the General Duty Clause provides protection from hazards not covered in the more industry specific standards.I know most of us are used to dealing with more spectacular-looking confined spaces with much more hazardous products; however, this one was just as deadly. It drives home the point…
a confined space is a confined space, no matter how benign it may appear, regardless of whether it’s located at the workplace or the homestead.
If it meets the definition of a confined space, it should be treated as a potential “permit-required confined space” until it is proven that there are no hazards present, or the hazards have been properly addressed.
(Click here to OSHA Fatal Facts)Manslaughter Charges Filed in Trench Death

Second-degree manslaughter charges have been filed against the owner of a Seattle construction company resulting from a 2016 trench fatality. This marks the first time a workplace fatality in Washington state has prompted a felony charge, according to the Washington Department of Labor & Industries.
On January 5, the company owner was charged by the King County Prosecuting Attorney’s Office, which alleges criminal negligence in the January 2016 death of a worker, who died when the trench he was working in collapsed.
“The evidence shows an extraordinary level of negligence surrounding this dangerous worksite,” said Mindy Young, King County senior deputy prosecuting attorney.
The company was fined more than $50,000 and cited for multiple safety violations in 2016 after an investigation into the incident.
“There are times when a monetary penalty isn’t enough,” Washington L&I Director Joel Sacks said in a Jan. 8 press release. “This company knew what the safety risks and requirements were and ignored them. The felony charges show that employers can be held criminally accountable when the tragedy of a preventable workplace death or injury occurs.”
The owner also faces a gross misdemeanor charge for violating a labor safety regulation with death resulting. His arraignment is scheduled for Jan. 18.
Two workers are killed in trench collapses each month, according to OSHA. The agency states that a cubic yard of soil can weigh as much as 3,000 pounds.
Source: www.safetyandhealthmagazine.com
RescueTalk™ (RocoRescue.com) has been created as a free resource for sharing insightful information, news, views and commentary for our students and others who are interested in technical rope rescue. Therefore, we make no representations as to accuracy, completeness, or suitability of any information and are not liable for any errors, omissions, or delays in this information or any losses, injuries, or damages arising from its display or use. All information is provided on an as-is basis. Users and readers are 100% responsible for their own actions in every situation. Information presented on this website in no way replaces proper training!