As an employer with permit-required confined spaces, you’ll need to determine if your rescue team or selected rescue service can truly “walk-the-walk” when it comes to confined space rescue. OSHA’s Permit Required Confined Space Standard (1910.146) is “performance-based” – meaning it’s all about capabilities when the stakes are high.Conducting a performance evaluation of your rescue service is a vital component in determining their true capabilities as well as fully meeting the performance requirements of 1910.146.
The Dilemma
Determining the adequacy of the team’s rescue capability can present a dilemma for many employers. That is, does the employer have the depth of understanding in technical rescue required to administer an accurate, meaningful performance evaluation? Do they know what to look for in terms of proper equipment use, efficiency, compliance with industry standards, and required safety systems – just to name a few. If not, is it then possible that the team may not be able to affect rescue when the need arises?As we know, it’s quite easy to demonstrate a rescue capability for a very “straight forward” situation. This is what we call a “Dog and Pony Show.” They tend to be very controlled and scripted to ensure that everything goes smoothly. Unfortunately, when there’s an actual emergency, it seems the victims never get a copy of the script. Unless the rescue team or service is prepared for the “other than straight forward” rescue, the operation has little chance of going smoothly. There are still way too many incidents involving injury or death to would-be rescuers that can be directly attributed to lack of proficiency in the type of rescue being attempted.
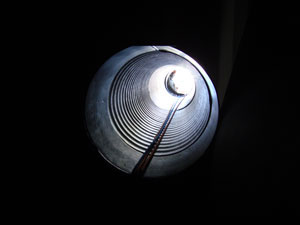
The Guidance
Fortunately, Appendix F (Non-Mandatory) of 1910.146 provides guidance for employers in choosing an appropriate rescue service. It contains criteria that may be used to evaluate the capabilities both of prospective and current rescue teams. For all rescue teams or services, the evaluation should consist of two components:An initial evaluation, in which employers decide whether a potential rescue service or team is adequately trained and equipped to perform permit space rescues of the kind needed at the facility and whether such rescuers can respond in a timely manner.
A performance evaluation, in which employers measure the performance of the team or service during an actual or practice rescue.
Another way to break down these two evaluation components is something like this… (1) The initial evaluation is to determine if the rescue service can “talk-the-talk”; and, (2) the performance evaluation is to determine if the rescue service can “walk-the-walk.”
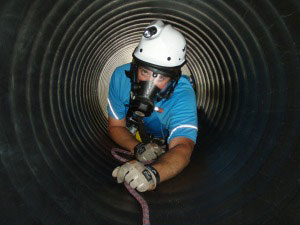
Additionally during the initial evaluation the employer should determine if the rescue service/team has the necessary equipment to perform rescues. This includes both technical rescue equipment and if a space may pose a significant atmospheric hazard which requires entry rescue, does the team/service have adequate supplies of SCBA [or SAR].
ROCO NOTE: Another aspect often overlooked is HazMat capabilities… does the team have the proper training and PPE to protect themselves from the particular hazards they may face? Can they deal with de-con issues that may result from exposure? Or, as the employer, will you provide the appropriate PPE and decon?
Finally, the employer should evaluate if the rescue team/service has the technical knowledge for vertical rescues in excess of five feet, the knowledge of rope work or elevated rescue, if needed, and the necessary skills for medical evaluation and patient packaging. Other than the visual and/or physical review of the rescue equipment; and, if necessary, emergency breathing air, the initial evaluation of the team/service is primarily completed through interviews and a review of training documents. In other words, can the team or service “talk-the-talk”?
Therefore, it is simply not enough for an employer to rely on the initial evaluation. While it’s a good start in narrowing the field of prospective rescue team/services, it is incumbent on the employer to determine if the rescue service can indeed walk-the-walk. And the only way to ensure that is to complete a performance evaluation during an actual or practice rescue from the actual or representative types of spaces that they may be summoned to.
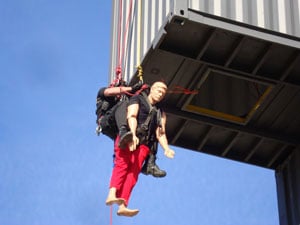
The Third Party Advantage
Performance evaluations can be administered to a prospective rescue service, or as a periodic evaluation of current rescue services. As an option, an employer may choose to use a third party that has extensive experience in this type of rescue.This is especially beneficial when employers may not have the in-house expertise necessary to administer an accurate evaluation, or for employers who are more comfortable with having a third party evaluation as a documented, independent, and unbiased record of the rescue service/team’s capabilities.
As an independent evaluator, Roco has conducted these team (TPE) and individual (IPE) performance evaluations for many years using specific grading criteria. It is a valuable tool for the employer to ensure and document that the selected rescue team/service (whether an outside service or in-plant team) has the required proficiencies for rescue at their facility. These TPE/IPEs also provide a degree of refresher training that will help bring the team/individual up to the level they need to be.
In rare instances, our recommendation may be that the team requires more than spot training in order to meet an acceptable level of proficiency. Another benefit of third party TPE/IPEs is that it may be an opportunity for the evaluator to recommend minor changes in equipment or techniques that would enhance the capability of the team. In fact, Section B of Appendix F states,
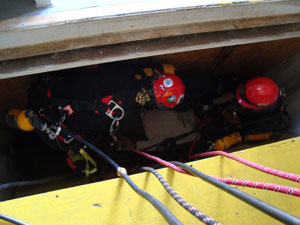
Another area where third party evaluations are beneficial is when contractors will be providing their own rescue capability. Some host employers mistakenly believe that theyare relieved of all responsibility when the contractor’s employees are performing the entries. But 1910.146(c)(8) and (9) place reciprocal responsibilities on both employers to each other. This includes the host employer informing the contractor that permit space entry is allowed only through compliance with a permit space program meeting the requirements of 1910.146, and the contractor informing the host employer of the permit program it will be following.
Although this paragraph of the standard lacks specific direction, it certainly contemplates that the host employer cannot turn a “blind-eye” to deficiencies in the program presented by the contractor – including insufficient rescue capabilities. A team performance evaluation would be helpful in determining the contractor’s ability to provide rescue services for their employees. While some host employers may be qualified to evaluate contractor’s technical rescue capabilities, that is usually not the case.
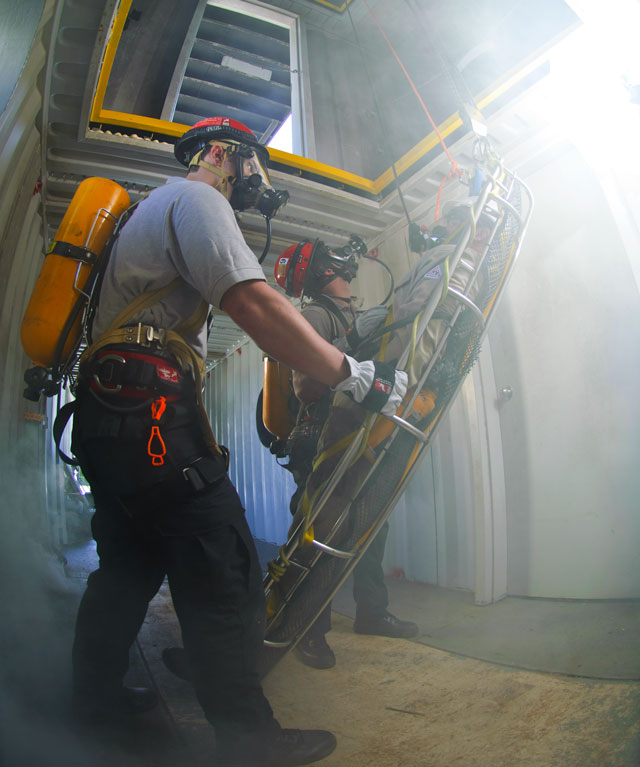
Keeping Skills Fresh
Employers must also realize that technical rescue skills are very perishable. While a team or individual can successfully complete rescue training and attain a high degree of proficiency, regular practice is crucial to maintaining these skills. Unfortunately, all too often, the time and resources required to maintain this level of proficiency are not provided. How quickly these skills erode will vary. However, even with the most experienced rescuers, they will eventually lose their edge if practice time is not provided. For newer rescuers that complete their training but don’t the chance to practice fairly soon, their skills can erode at an incredibly fast rate.The degree of difficulty for the anticipated rescues must also be considered. When more complex rescues are involved, teams may require even more training and practicetime to maintain their level of expertise. And, while a training certificate is good to have, the only way an employer can truly know if the rescue team/service meets the OSHA performance requirement for confined space rescue is by completing a properly administered performance evaluation.
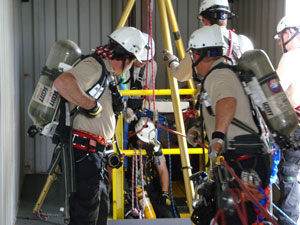
If you would like additional information on a documented Team Performance Evaluation for your rescue service, please contact Roco at 800-647-7626.